Three key success factors for effective co-creation with Pfizer
Insights into the collaboration with BAUMANN Engineering in process optimization
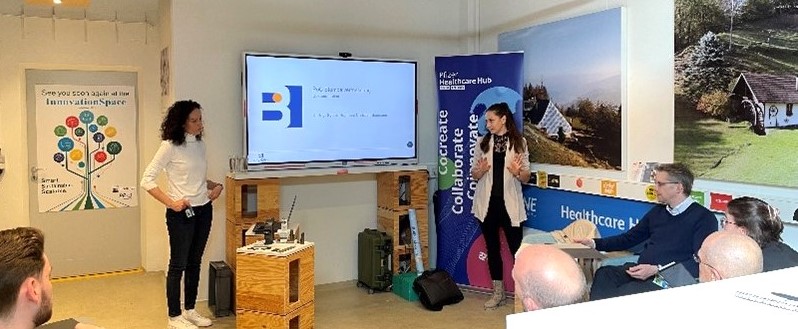
To continuously drive innovation in the production processes at Pfizer’s Freiburg manufacturing site, the Pfizer Healthcare Hub connects internal departments with external solution providers. One proven partner for process optimization projects is the engineering firm BAUMANN Engineering OHG. With their expertise in engineering, additive manufacturing, and automation, BAUMANN’s engineers and technicians develop solutions to optimize production and packaging processes at the Freiburg site. The goal is to bring processes up to the latest technological standards and keep them efficient and scalable.
BAUMANN Engineering works closely with Pfizer on both complete solutions – from initial task definition to implementation – and on individual work packages. The conditions for successful collaboration since 2020 are illustrated through three key projects: the High-Tech Adapter, automated punch inspection, and the AI-supported container check.
“For us, the BAUMANN team is a model collaboration partner we’ve enjoyed working with repeatedly since 2020. They quickly grasp the task at hand, respond flexibly to our change requests, and present well-thought-out solutions in a short amount of time,” says Oana Stürz, Innovation Engineer at the Pfizer Healthcare Hub.
3 key qualities of co-creation partners
Key aspect 1: Collaboration begins with task definition
Example: The high-tech adapter project
The supply of raw materials is still partially manual – a process that is both time-consuming and costly,” says Pembe Gül Bilir, Innovation Engineer at the Healthcare Hub Freiburg. “Our colleagues were looking for an automated solution that would also enable analysis and sampling at this stage of the process.” She took on the challenge of developing an automated material feed system with integrated process analytics. Together with the specialist department and Sybille Hopman, one of the two managing directors of BAUMANN, she defined the task.
“We like to be involved as early as the problem-definition phase, because the best solutions emerge through close collaboration with our partners,” explains Hopman. “When we discuss challenges together from the outset, we not only gain a better understanding of the specific requirements and workflows, but also develop a shared perspective. This leads to new approaches and technically sound solutions.”
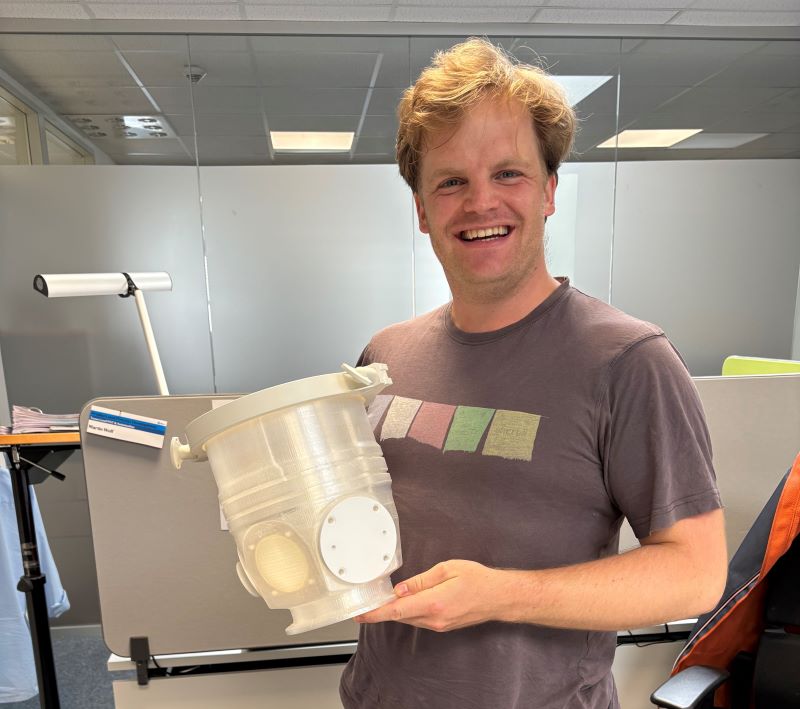
The BAUMANN team is currently developing specialized adapters that automate the material feed process while simultaneously integrating process analytics. Following a successful test with a 3D-printed prototype, twelve metal adapters are planned for production and will be deployed at the Freiburg site.
Key aspect 2: Coverage of all project phases
Example: punch measurement project
The punches used in tablet pressing must be regularly measured by trained personnel using a specialized dial gauge—a time-consuming manual task that was targeted for automation.
To address this, the BAUMANN team developed a solution involving automated camera technology, punch trays, and a robotic arm.
This project was of particular interest to Christian Baumann:
“We supported the punch measurement project from planning through to manufacturing and installation. For the various components, we were able to draw on partners from our network and integrate state-of-the-art technologies.”
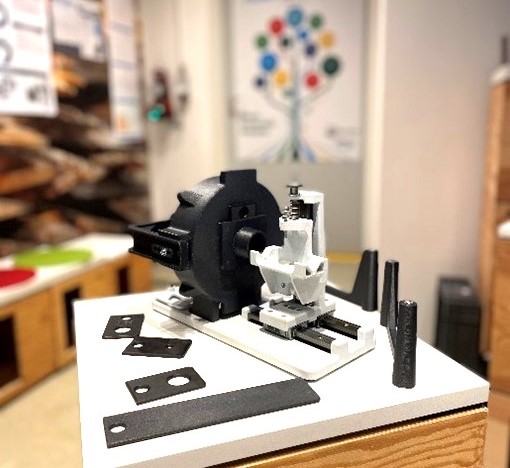
What makes this solution particularly interesting is its high scalability: nearly every tablet is stamped, which means the automation of punch measurement can be extended to other departments and production sites in the Pfizer network.
Key Aspect 3: Flexible models for co-creation: support for projects or individual work packages
Example – Artificial Intelligence Container Check
Another step toward process optimization: The visual inspection of cleaned bulk and powder containers was to be replaced by a fully automated container inspection station. BAUMANN Engineering developed an initial concept and CAD design, which served as the foundation for the development of an optical inspection system.
Learn more about the Artificial Intelligence Container Check
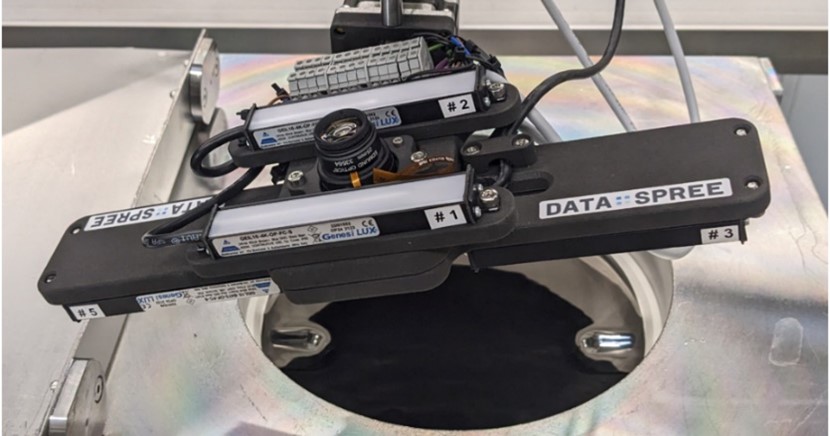
BAUMANN provides support for individual work packages or process steps, accompanies projects from the initial idea through to implementation and beyond, or offers consulting services—for example, in the Benchtop Feedframe pilot project or the optimization of blister embossing.
“Our collaboration with Pfizer is a partnership of equals. We value the open communication with contacts from both the Healthcare Hub and the specialist departments. It’s also incredibly valuable that the departments actively contribute solution ideas, which we then refine together. This results in outcomes that are both technically sound and perfectly aligned with process requirements,” says Christian Baumann.